How to run a laboratory cold room safely
Laboratory cold rooms are sensitive environments delivering critical services. Unlike ordinary storage solutions, lab cold rooms must be carefully maintained to ensure items remain safe to use and staff are protected from harm.
Problems with your cold room will have a devastating impact on the wider work of your laboratory. It’s crucial you understand how to manage your temperature controlled environment properly and preserve the quality of all items stored.
There should be appropriate documentation and training in place to guarantee your laboratory cold room is used correctly by all approved staff and its functioning closely monitored.
From staff training to resource management, here’s all you need to know to organise and manage your lab cold room correctly.
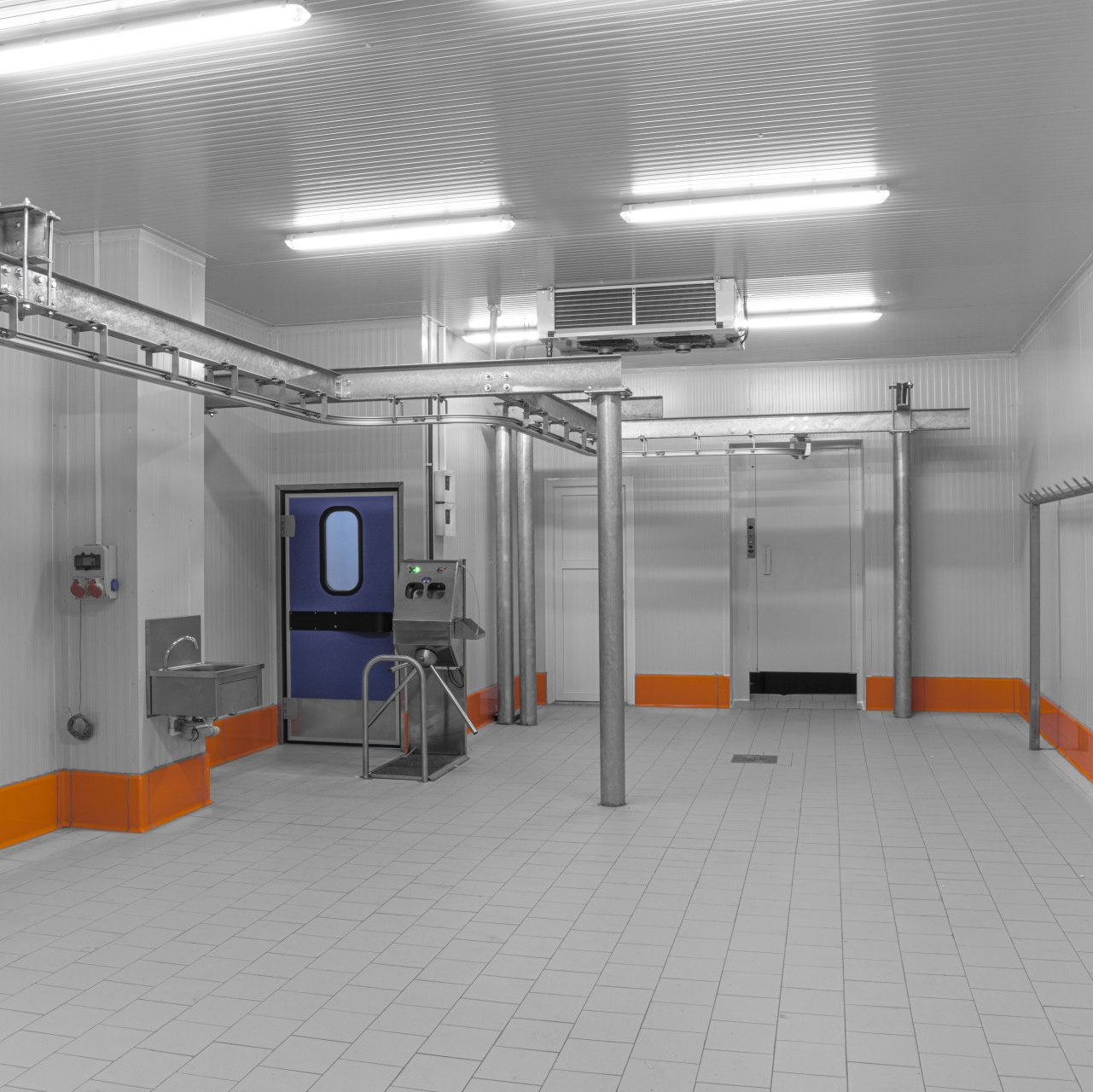
How to run a laboratory cold room safely
1. Maintain humidity: Ensure your cold room sustains the correct humidity level required to keep items free from damage. For most lab cold rooms the desired humidity range will be around 90 – 85%.
You will need to ensure there is a designated cold room manager who is responsible for regularly checking your cold room is operating as it should. Duties will include checking the humidity level remains constant. If the humidity level inside your cold room is discovered to have dropped below the required level, maintenance must be informed immediately so the source of the problem can be corrected. In the meantime, spray the floor with water from time to time whilst the temperature control is reset.
Depending on the degree and duration of the drop in humidity, further action may be necessary according to company guidelines,
2. Guard against mould: The development of mould is one of the damaging processes a cold room guards against. The cold room manager must also ensure checks are carried out to guarantee no existing or new items to be bought into the cold room
contain mould.
If any item with mould is uncovered, it must be removed from the temperature controlled environment and discarded according to company protocols.
3. Prohibited materials: For this reason, there should be a clear list of approved materials for cold room storage and cleaning. Prohibited materials include any products made from paper of any thickness. Items should be removed from paper packaging and stored in approved metal or plastic storage solutions.
If there are any paper products accepted by your company for storage, they should be put into a tightly sealed plastic container before entering the cold room. Always ensure staff understand the importance of checking the container is fully sealed before returning it to the cold room.
Corrosive bleach, hazardous dry ice and dangerous flammable materials are also prohibited.
4.Hazards: Closed air circulation in a laboratory cold room means there is a real danger of asphyxiation. To prevent accidental inhalation of dangerous products it’s important adequate staff training is in place. Any staff approved to use your temperature controlled environment should understand the potential implications of working in a space severely lacking in fresh air.
Staff must know how to follow safety procedures to keep themselves and others protected from harm meaning you will need to create a risk assessment for working in the cold room.
Potential hazards include flammable substances and dry ice which must not be stored in a cold room. Any spills must always be cleaned up immediately according to company guidance. Staff should be clear of the potential dangers which could develop from aerosols left suspended in the air following research.
5. Clean floors and orderly storage: Floors should remain free from obstruction and clean at all times. No storage should be left on floors and all staff must understand the importance of proper storage. Every item in your temperature controlled environment must be fully and clearly labelled.
Storage should be organised in a neat, orderly fashion on open shelving or carts. Always make sure there is adequate space inside your temperature controlled environment for staff to move around easily. Your policy should be to remove and discard any items found without labels.
Bleach should not be used for cleaning inside your temperature controlled environment because it will damage stainless steel storage. You will need to draw up a list of approved products for cleaning and ensure products for the clean room are kept separate from other general cleaning resources.
All discarded products must be disposed of outside the clean room according to company guidelines. There should be no rubbish collection facilities inside your clean room,
6. Scheduled supervision: The cold room supervisor will need to have an agreed schedule of checks which include: making sure the cold room door is properly closed, any issues are reported immediately and the space remains in a clean, safe condition.
For bespoke pharmaceutical or medical laboratory cold room design, installation or maintenance, call us today on: 0800 193 0076 to discuss your needs or
learn more about what we do.
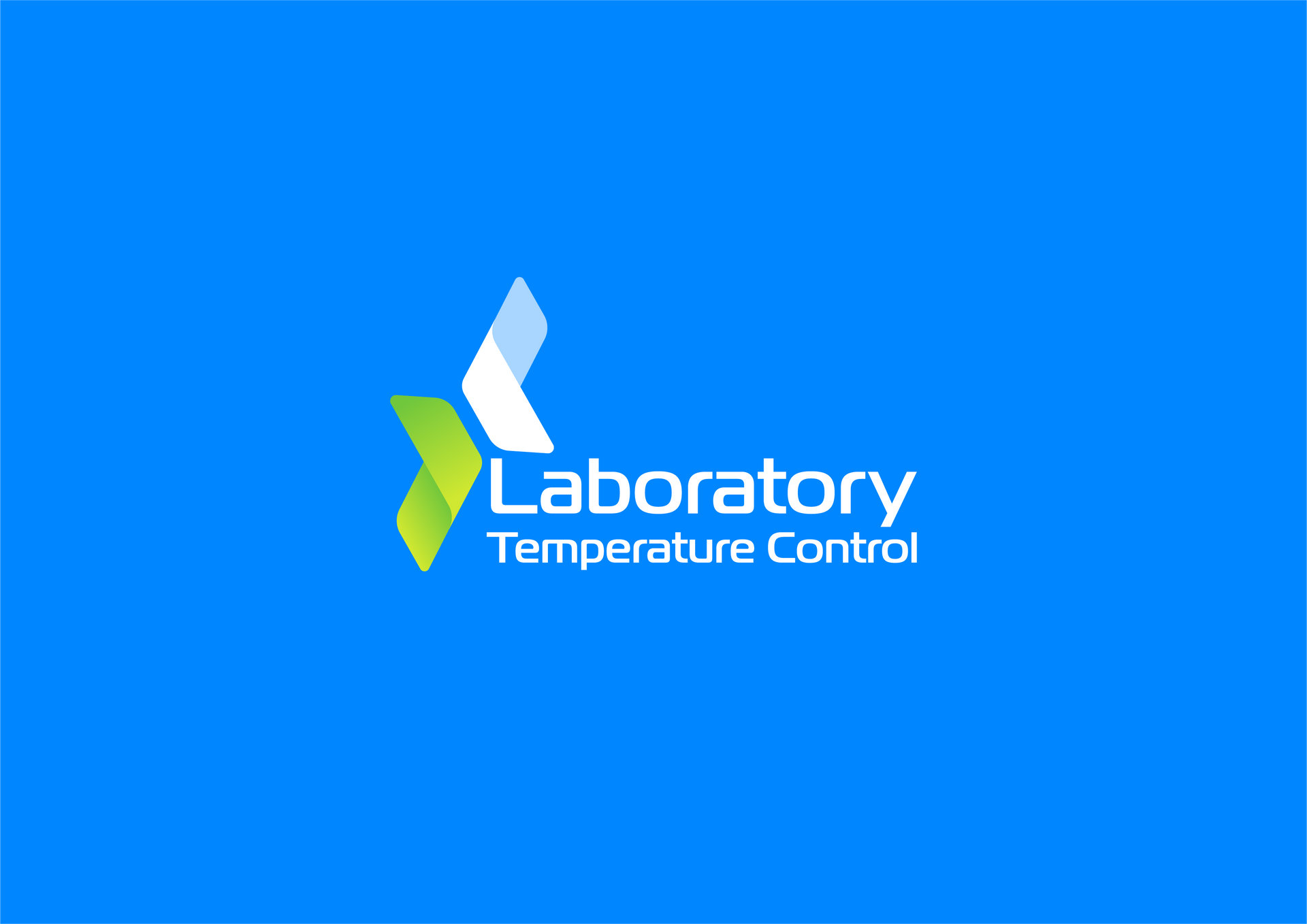
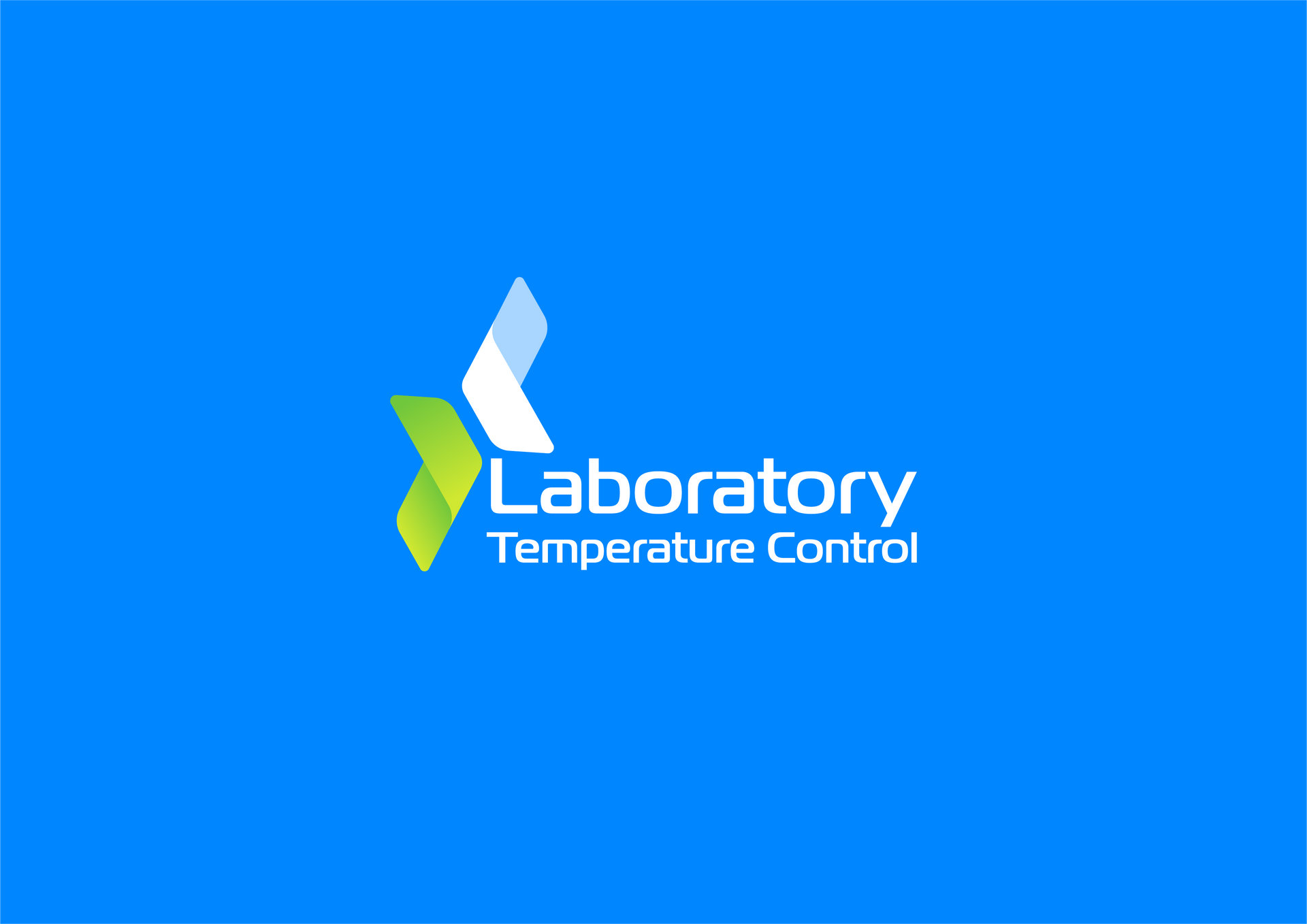
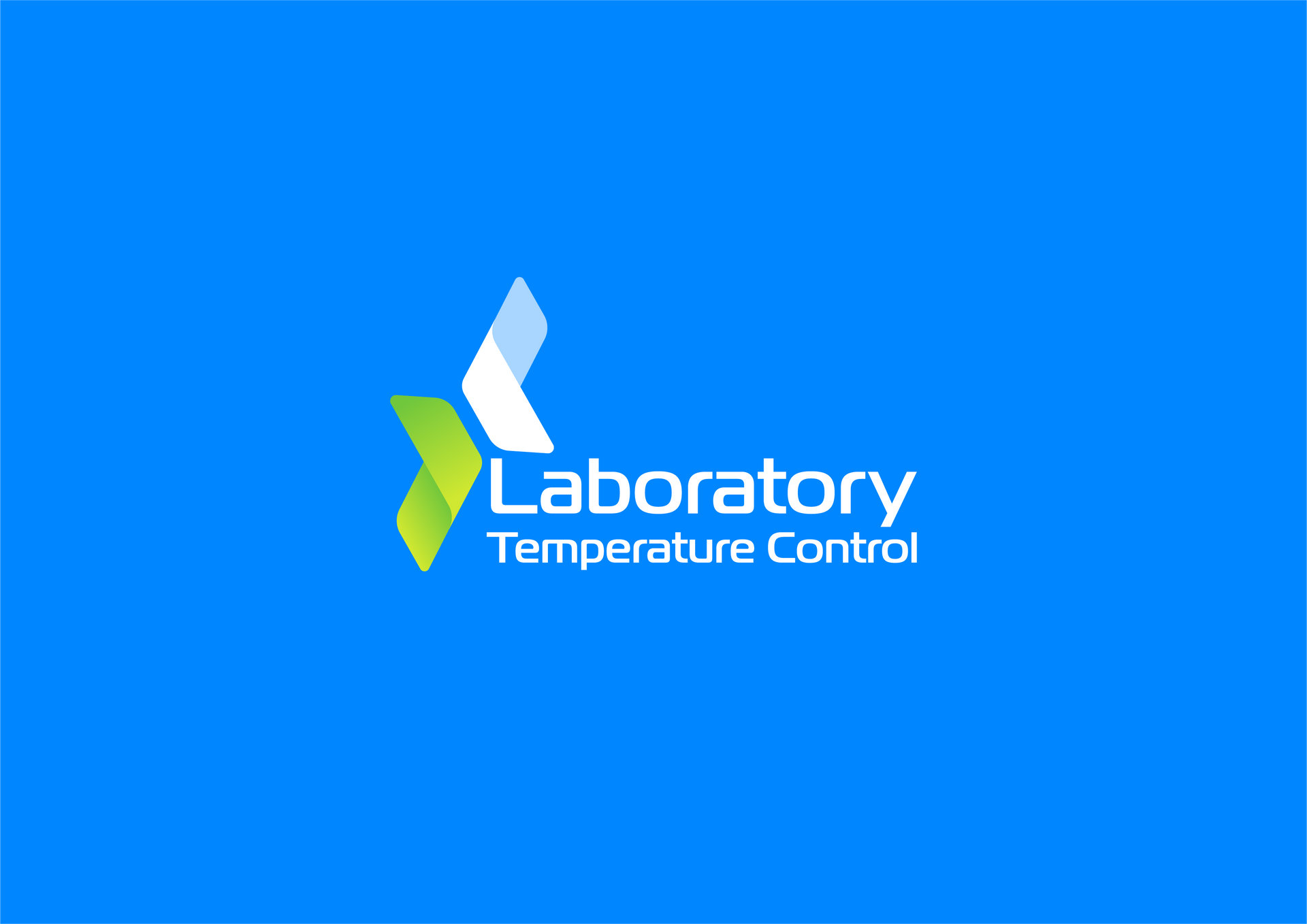
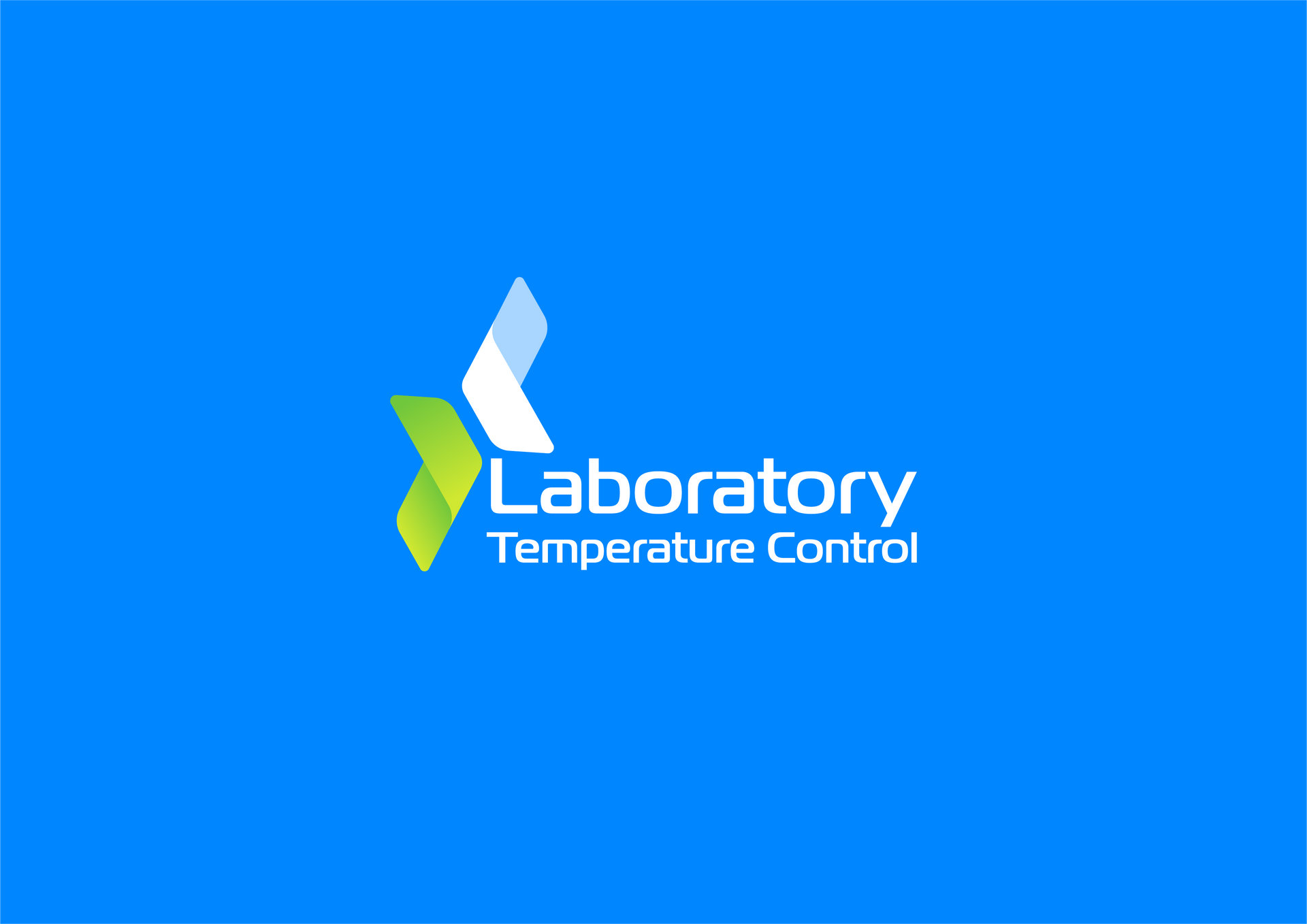
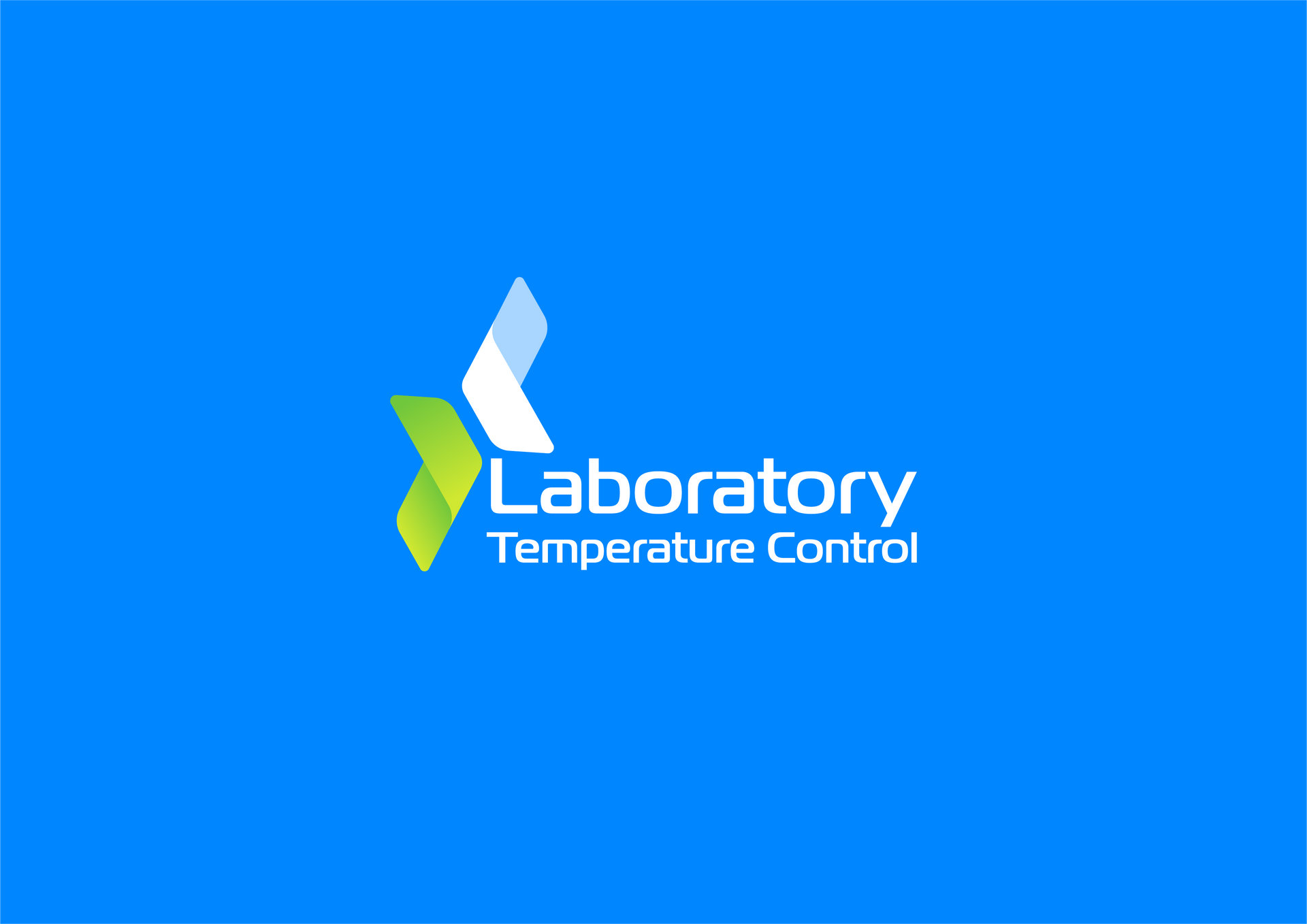
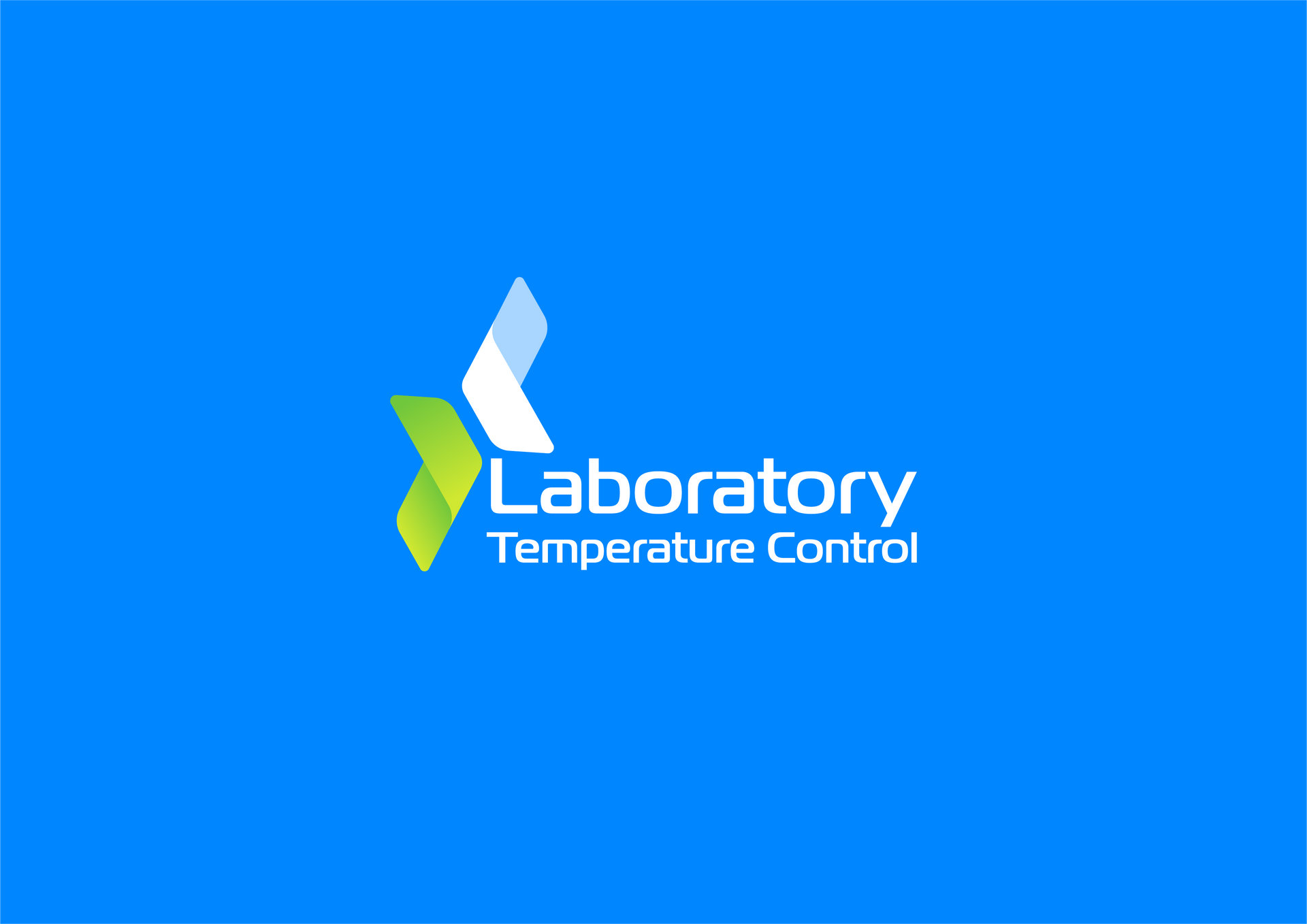
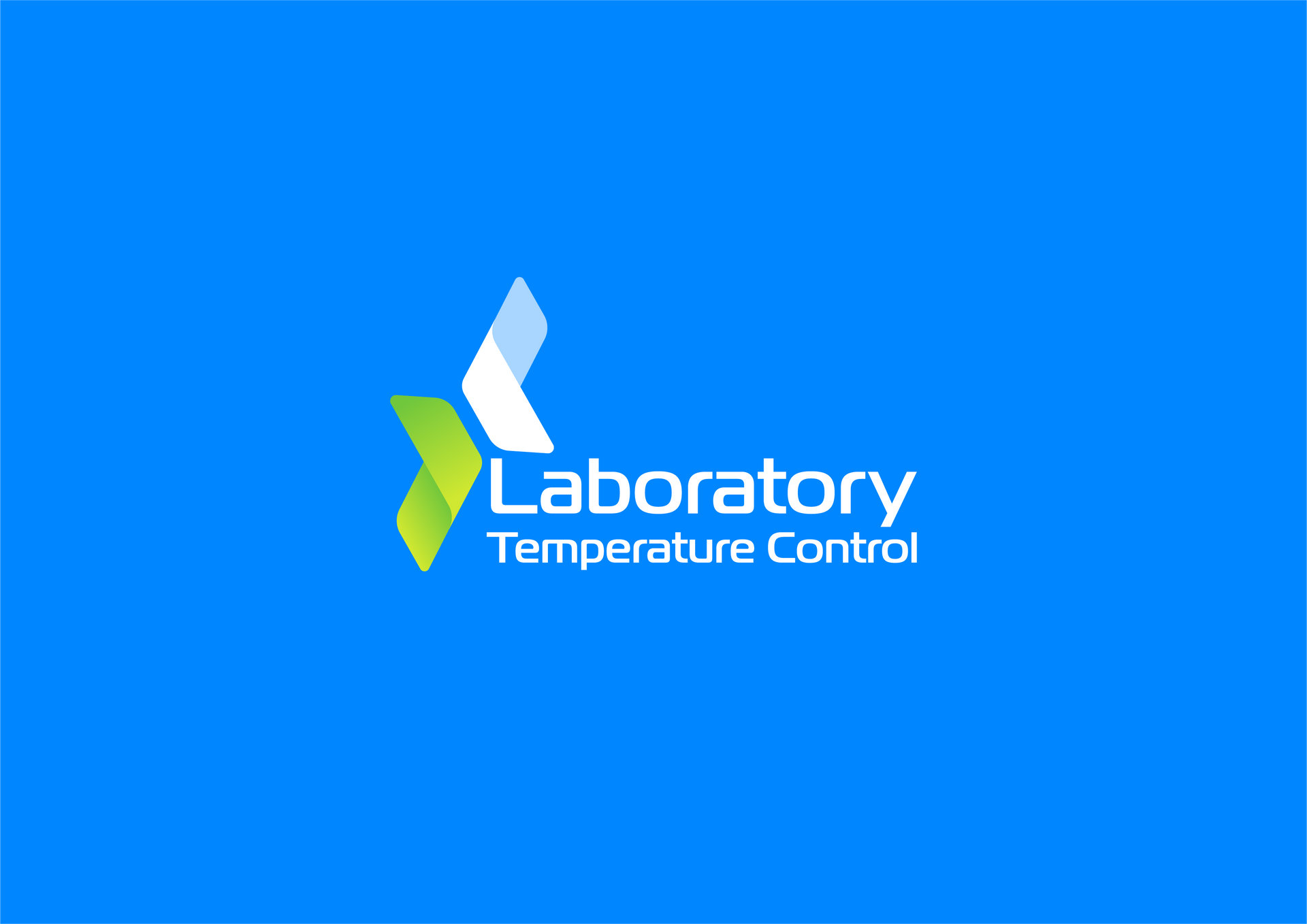
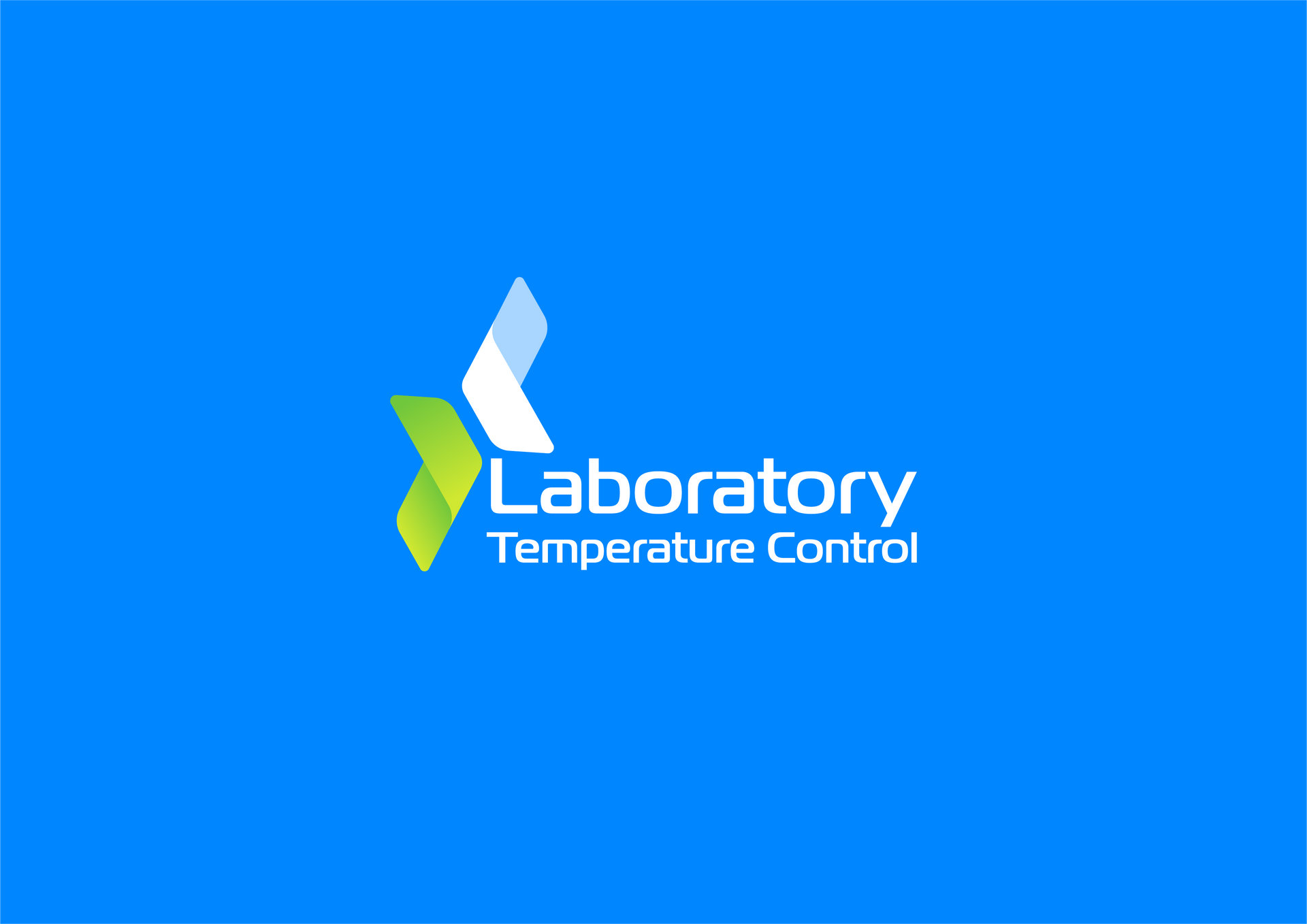
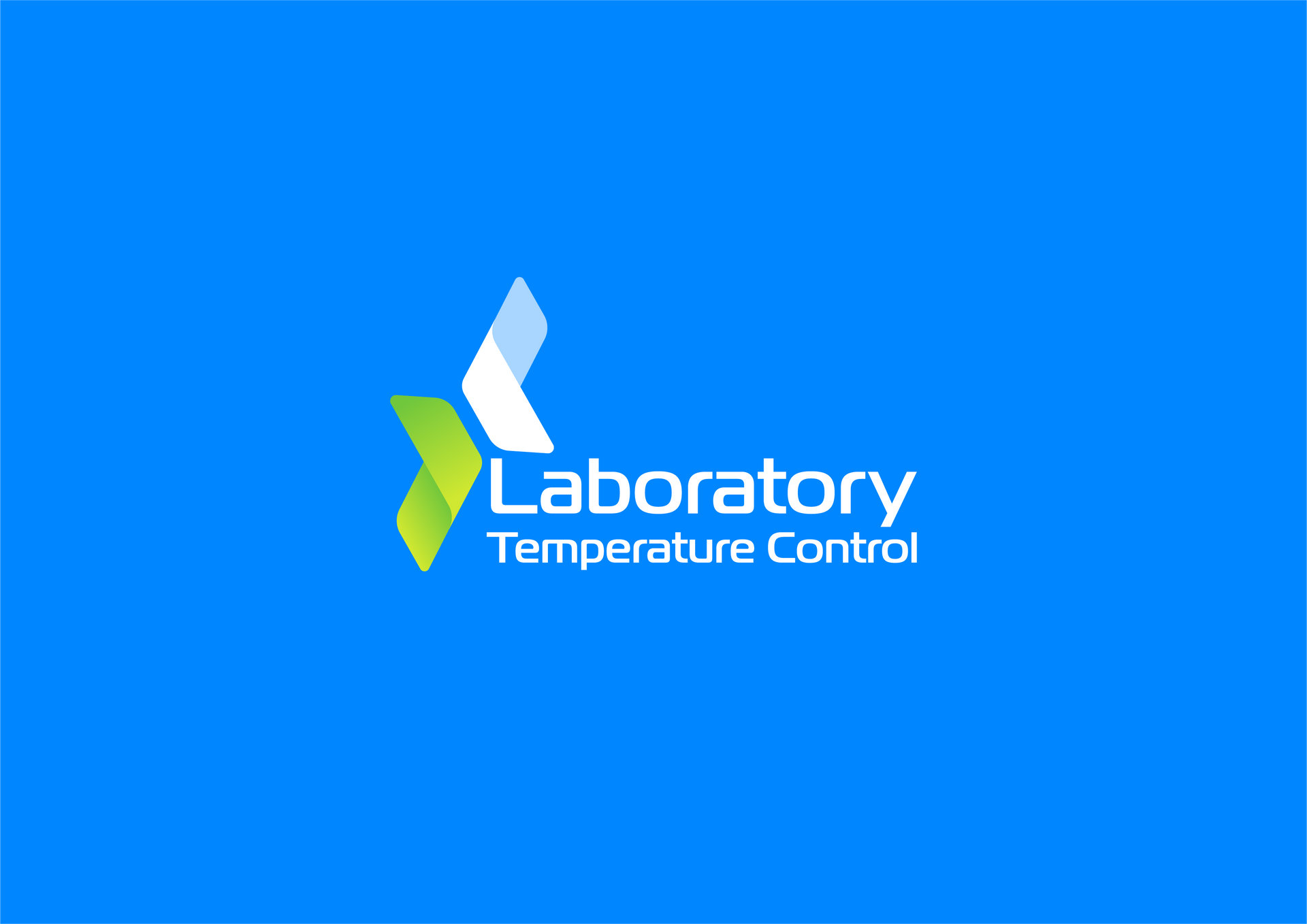
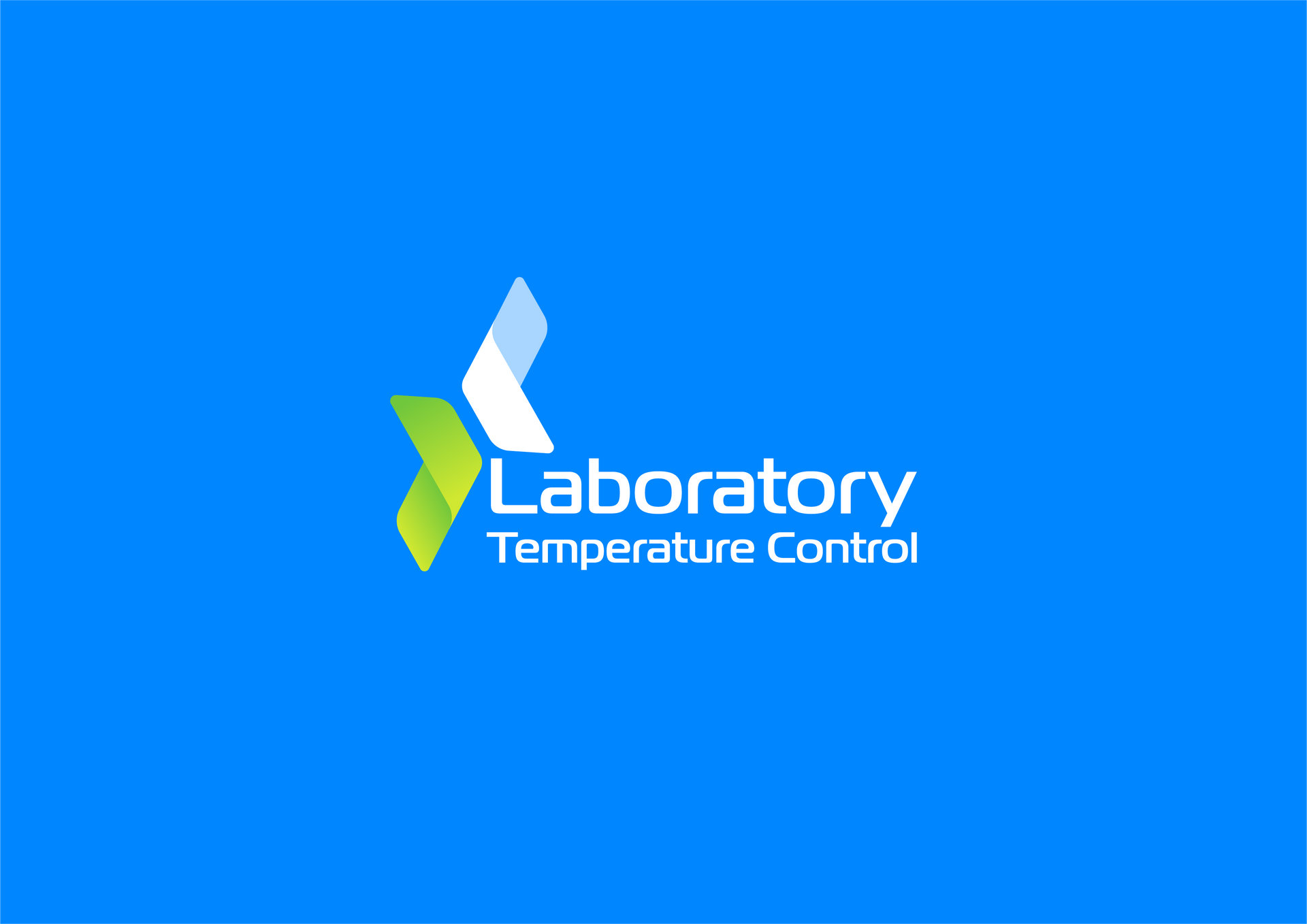
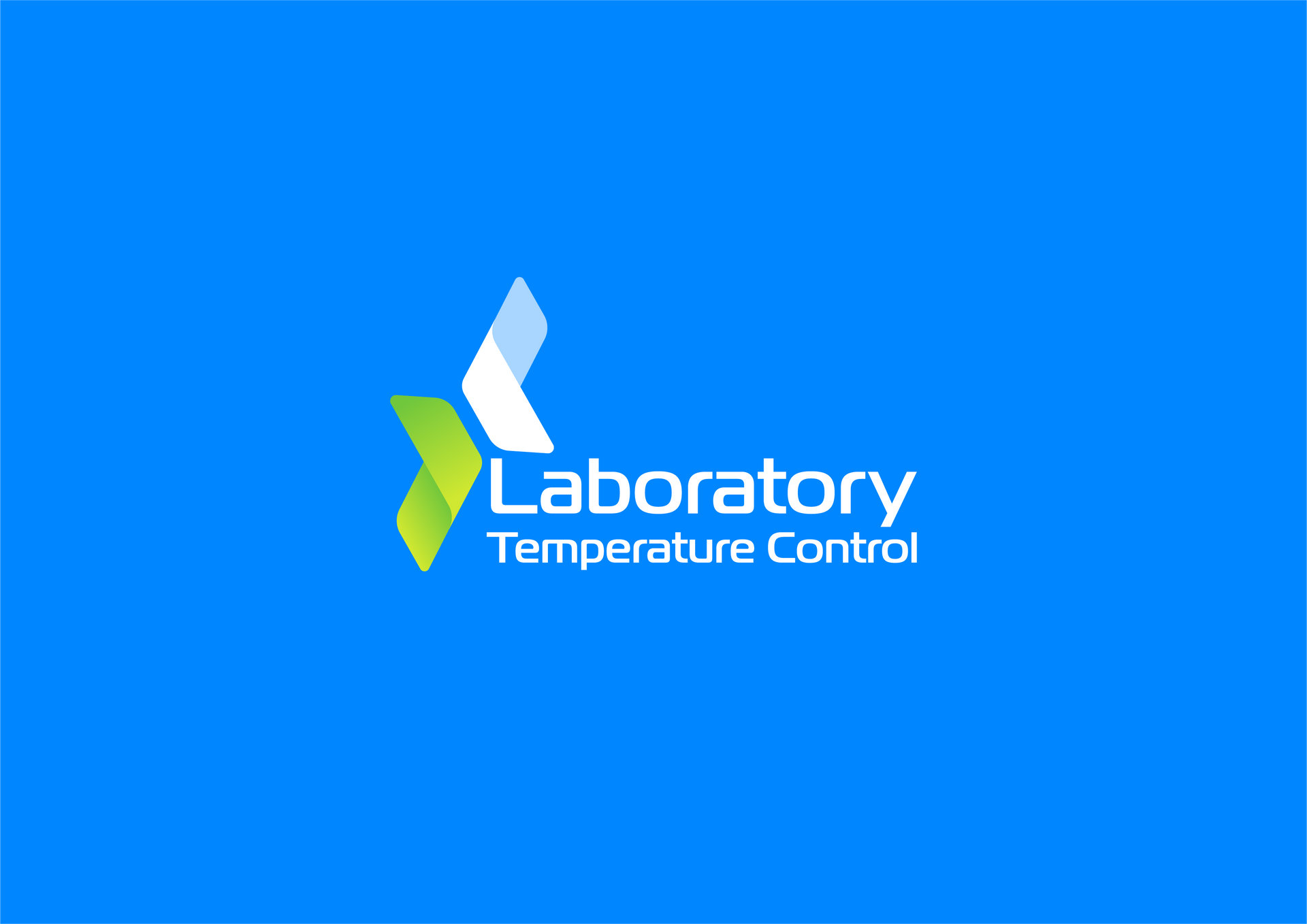
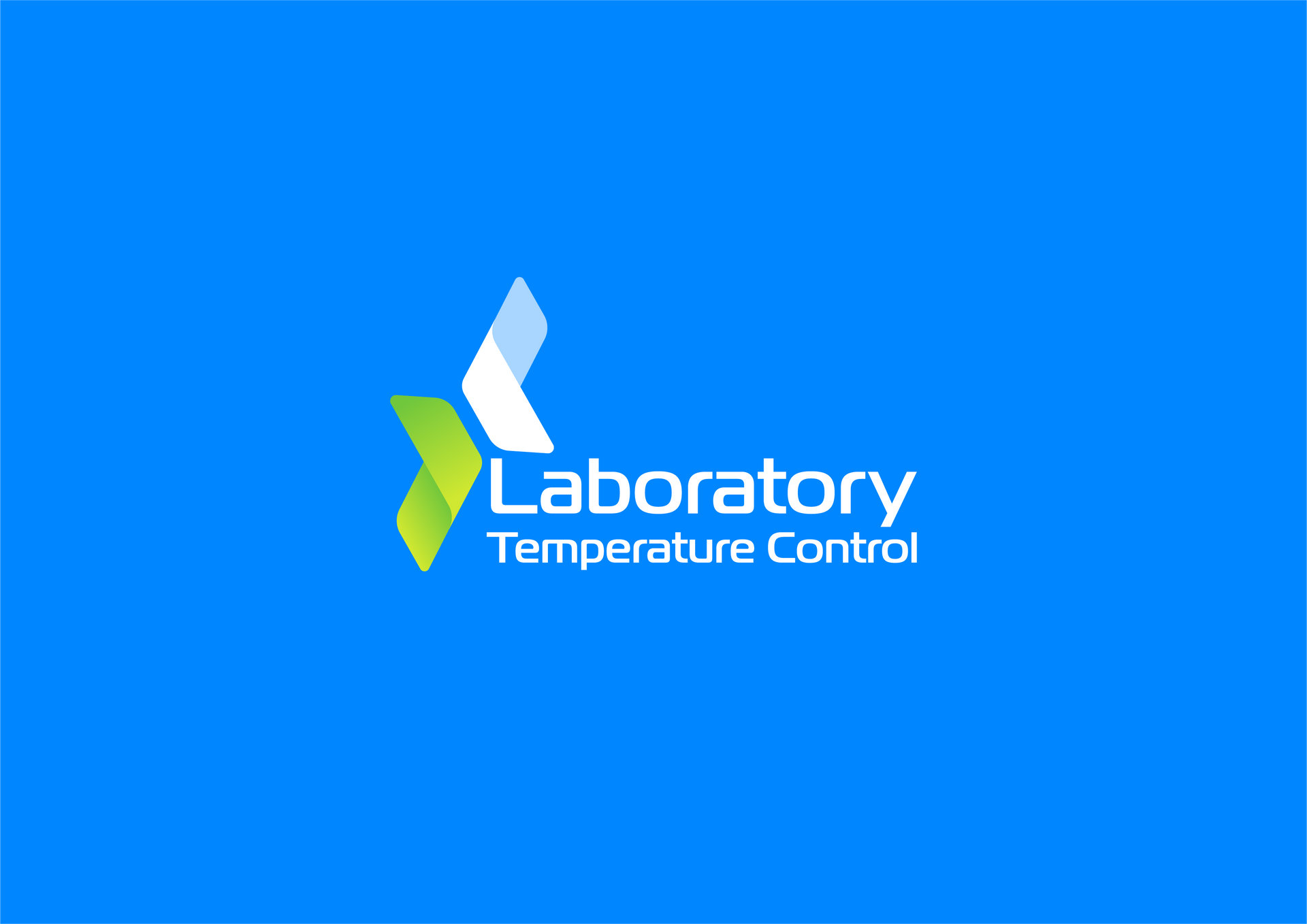
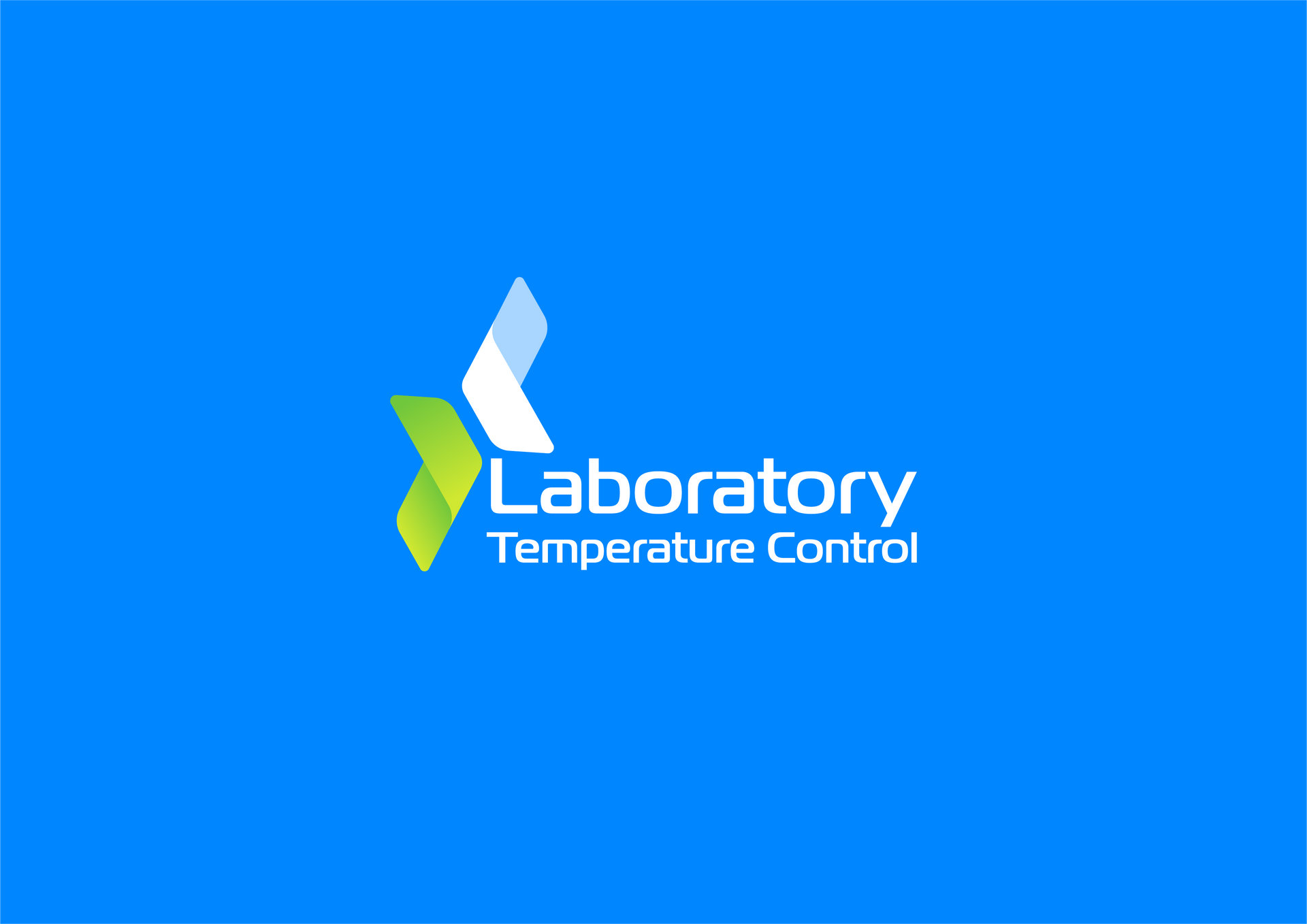
The Importance of Having a Breakdown and Service Contract in Place for Your Pharmaceutical Cold Room
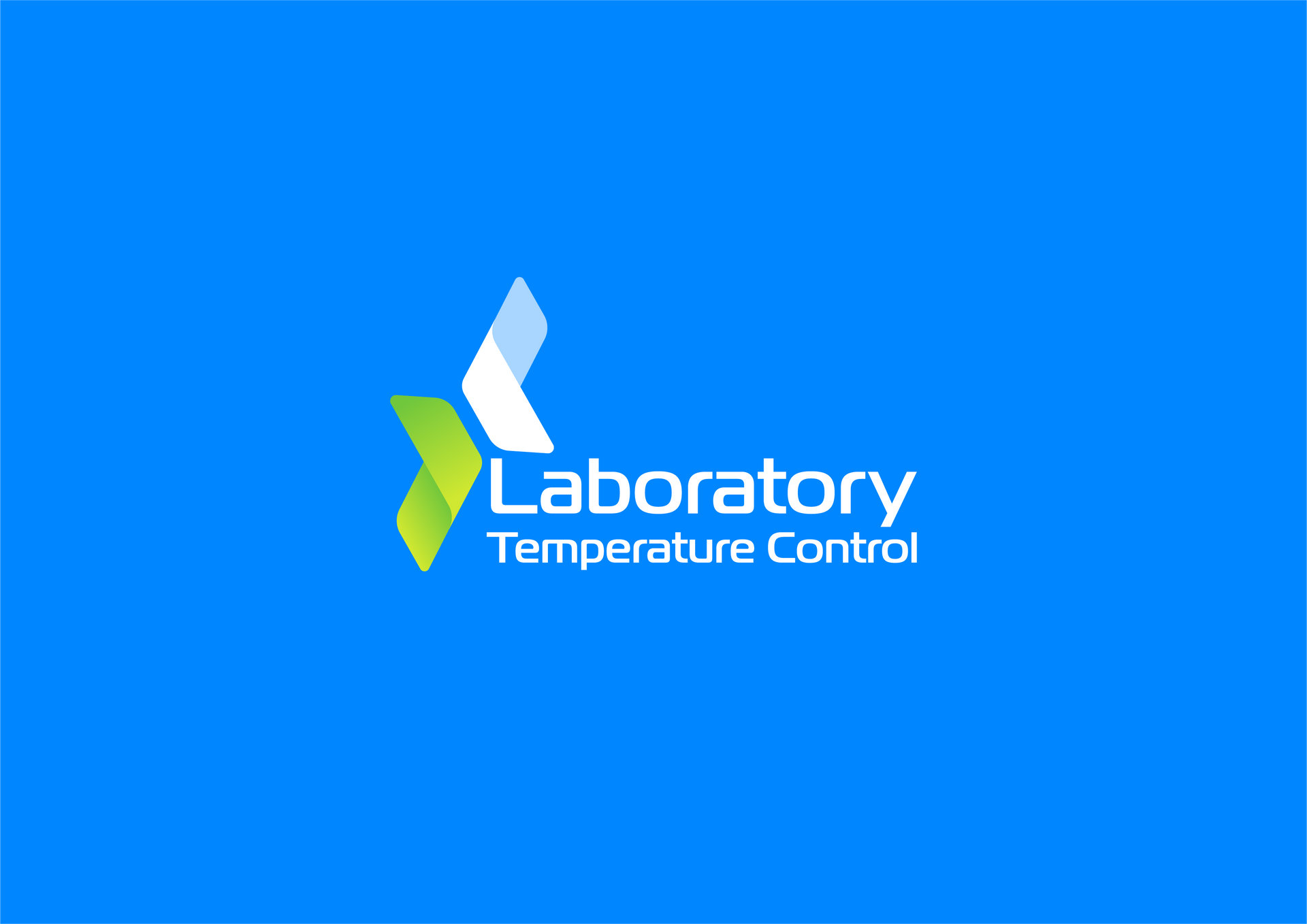
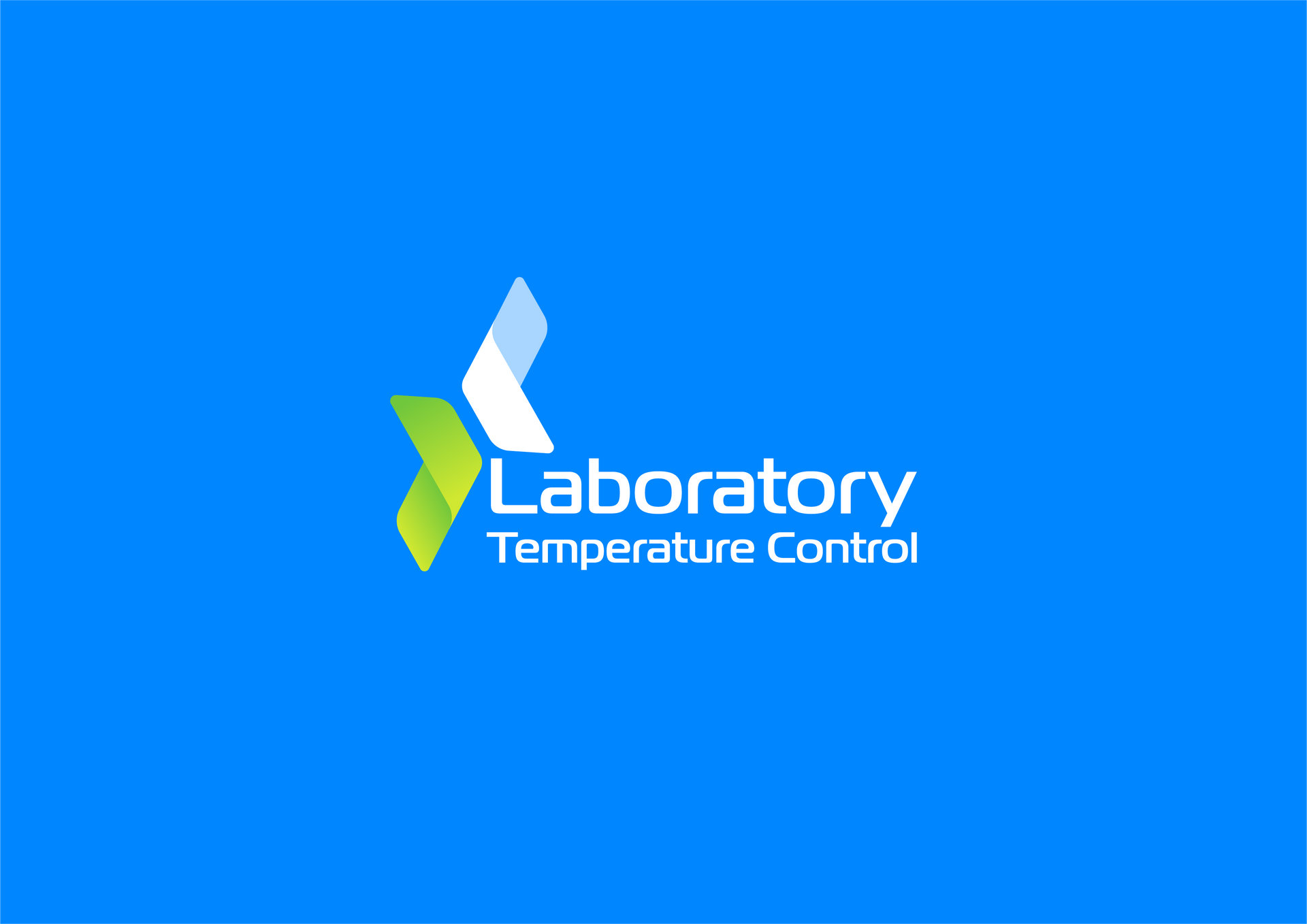
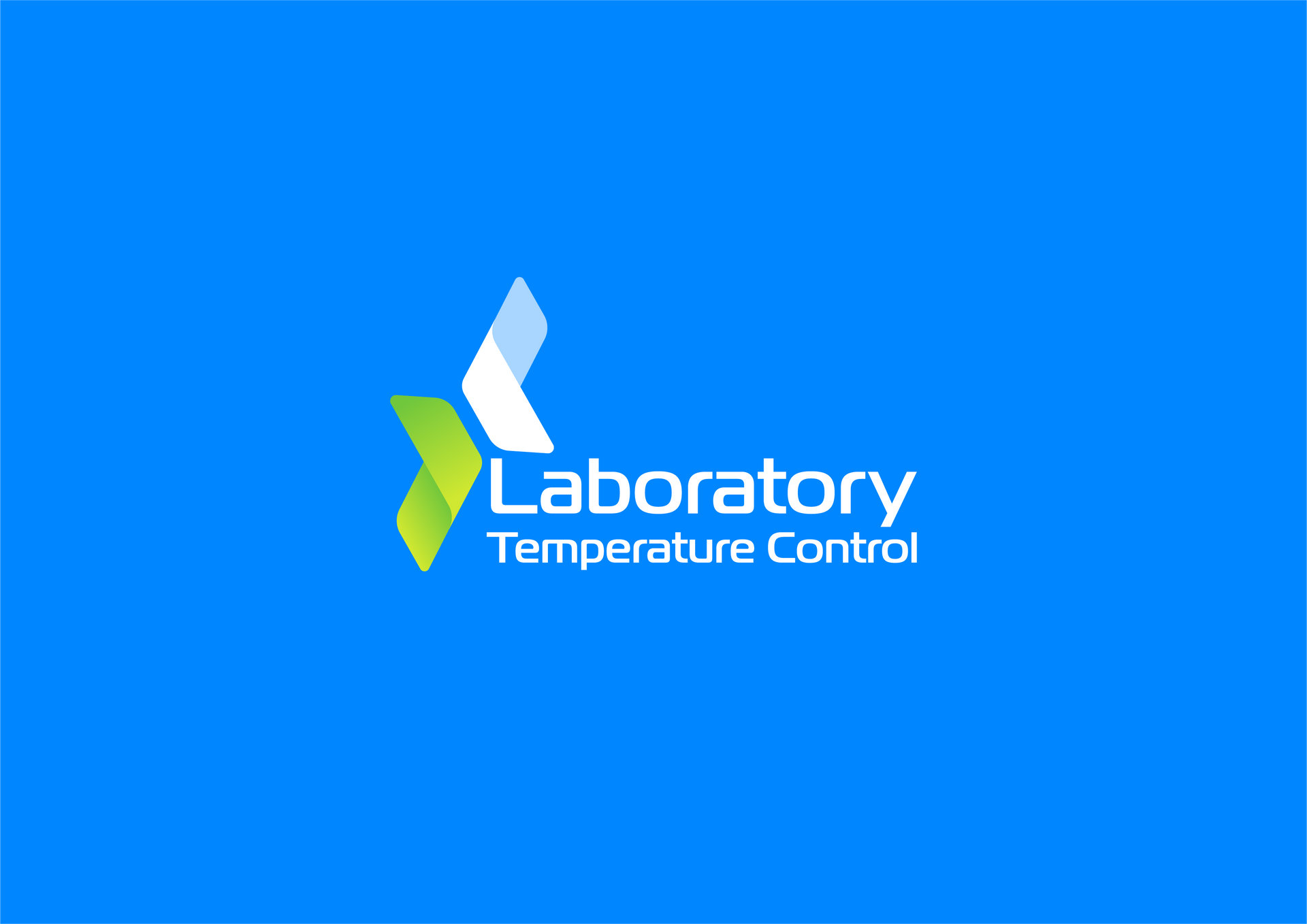
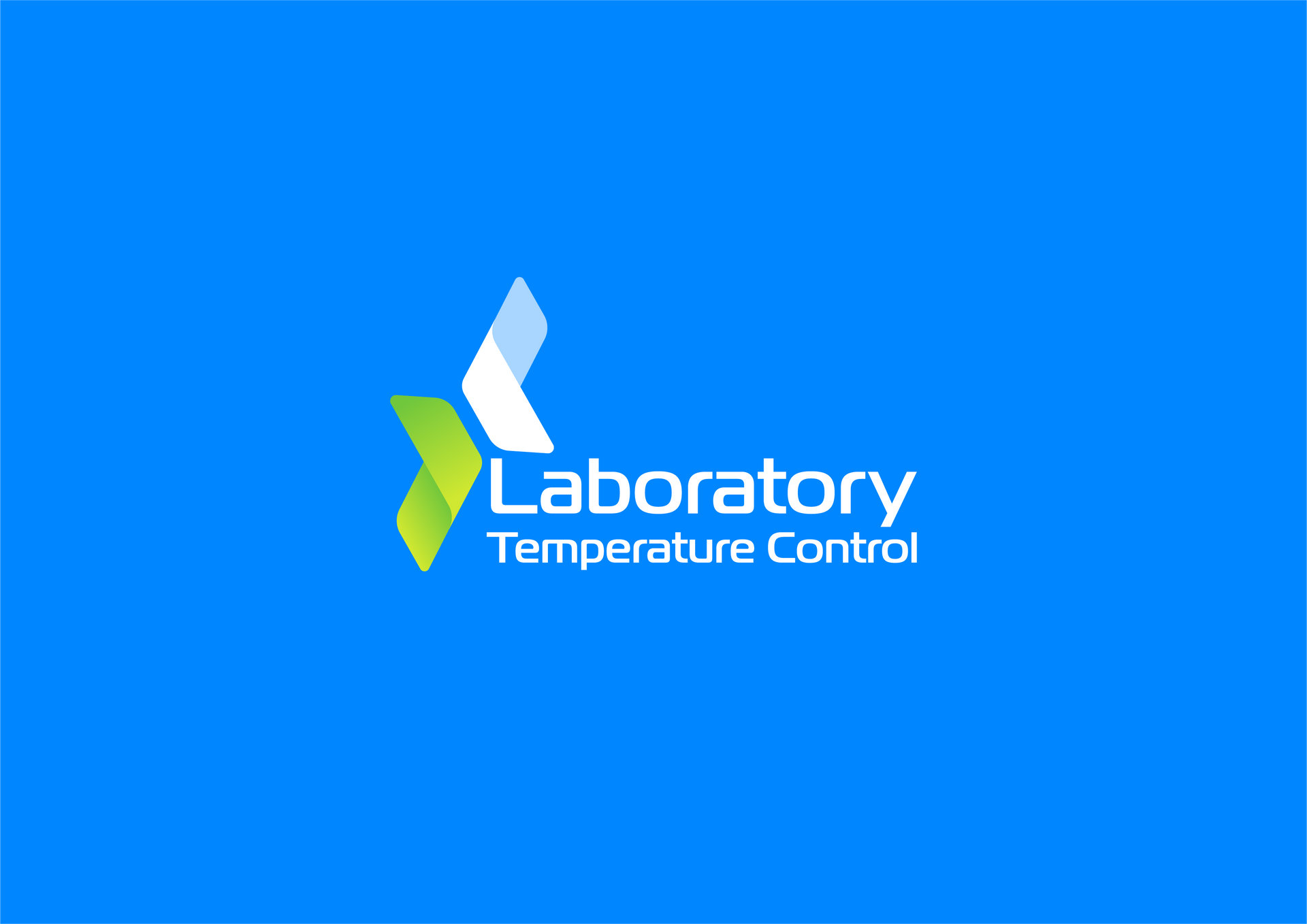